Powder Coating Overcomes Post Forming
Six Sigma methodology, open communication, and collaboration produce results for leading boat manufacturer.
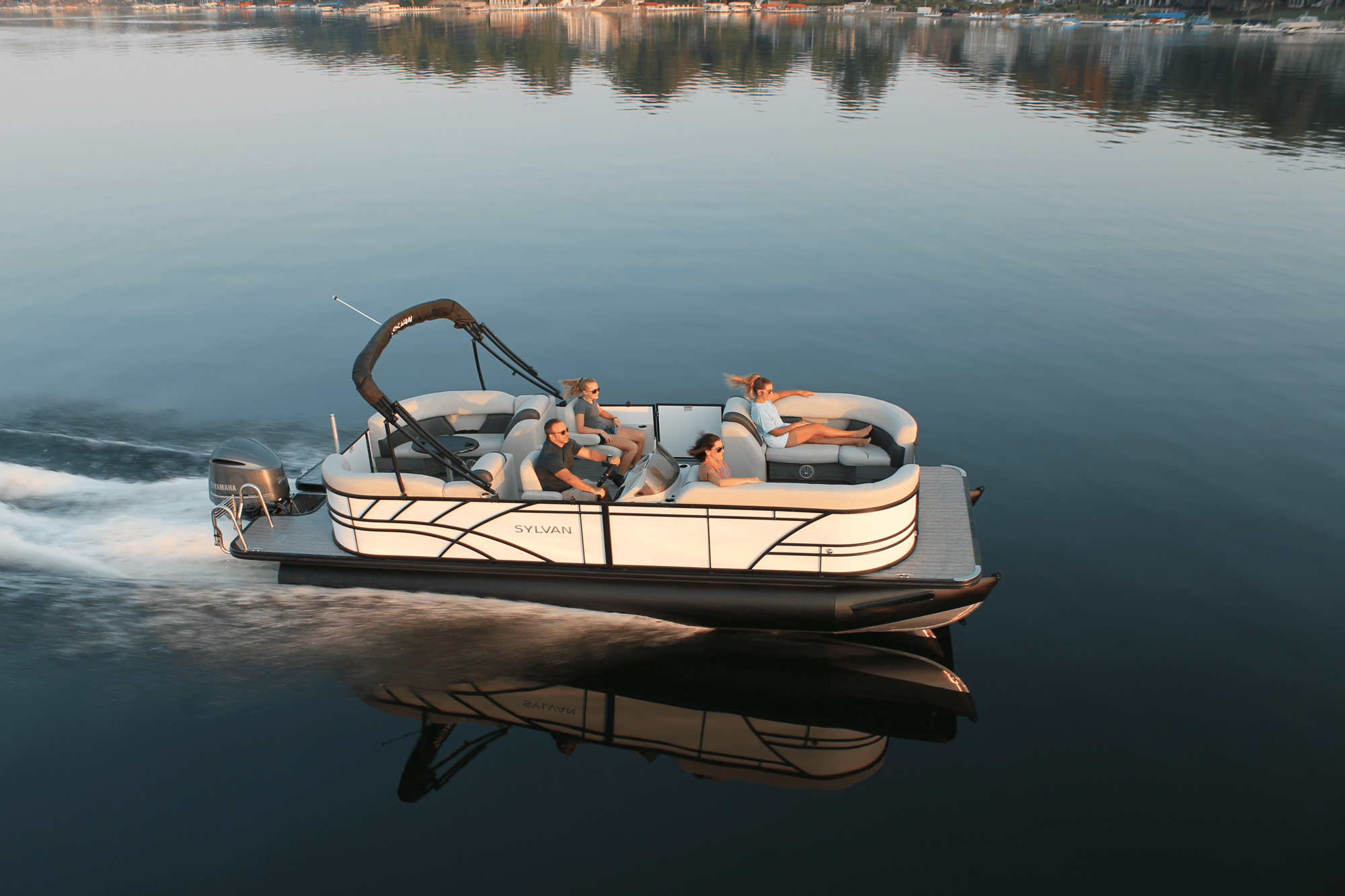
Seeking to eliminate defects produced during the post-forming of its anodized boat rails, Smoker Craft sought a powder coating partner to investigate an innovative solution.
Photo Credit: Smoker Craft Inc.
Innovation is often the product of collaboration. Much can be accomplished when problems are approached from multiple points of view. All too often in the finishing world, the surface finish is simply treated as a final step in the manufacturing process — a specification to be met.
A recent project between Winona Powder Coating Inc. (Etna Green, Ind.) and Smoker Craft Inc. (New Paris, Ind.) takes a much more in-depth approach and illustrates what can be accomplished when manufacturers, finishers and material suppliers work closely together. The project involved the post-forming of powder coated boat rails for Smoker Craft, Inc.
Smoker Craft Inc. is an Indiana-based boat manufacturer that builds, distributes and markets over 19,000 boats per year under the brand names of Starcraft, Smoker Craft, Sylvan, American Angler, Sunchaser, Starweld and Legend.
Powder coated rails have proven to be a bit of a white whale for the marine industry. Powder coating has often been looked to as a potential alternative to anodizing for railings, but previous attempts resulted in defect rates that were not viable.
Josh Drudge, vice president of operations at Smoker Craft Inc., says that past attempts at powder coating and then post-forming rails have been met with problems of peeling, cracking and subsequent corrosion of the substrate due to saltwater exposure. Yet the company still yearned for an alternative to black anodizing due to inconsistencies in the finish, particularly in areas where the boat railings bend.
“When you bend the rail, it actually changes the appearance of the anodizing,” Drudge says. “It almost looks fractured — it turns a white chalky color at the radius where you bend it.”
The company had dabbled with the amount of anodizing it used for the rails, toyed with the electrical charge and cleaning tanks, but ultimately found themselves spray painting the bends to try to match the rest of the anodized rail. Drudge says that the passage of time and improvements in technologies brought up the possibility of another run at powder coating.
“My thought was, ‘we can make it work, right?’” Drudge says. “If we could get partnered up with somebody that could handle it — and wanted to handle it.”
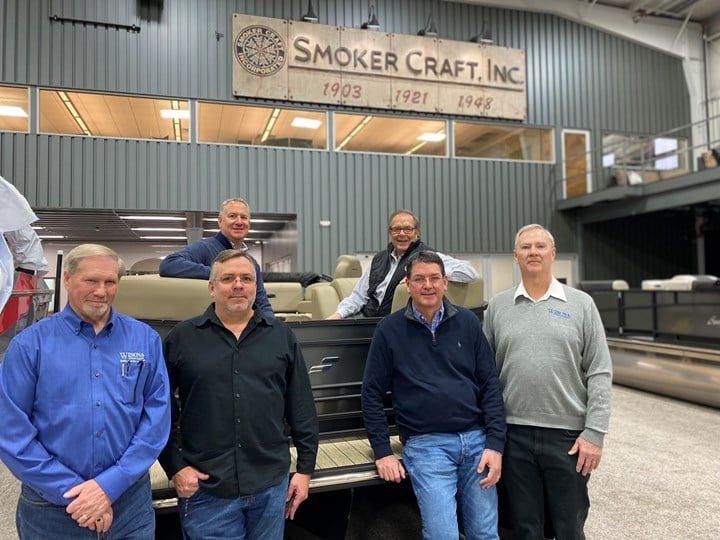
Counter clockwise: Larry Beals, VP Operations, Winona; Josh Drudge, VP Operations, Smoker Craft; Jamie Visker, Owner/CEO, Winona; Dennis Powell, Business Development Manager, Winona; Doug Smoker, President/CEO Smoker Craft; Peter Barrett, Senior VP/Marketing & Corp. Dev., Smoker Craft
Photo Credit: Smoker Craft Inc.
The right partner
Enter Winona Powder Coating Inc. Originally founded in 1974, Winona is a leading supplier of powder coating services to large industrial companies throughout the Midwest. The company was purchased by CEO Jamie Visker in 2002 and expanded to a 167,000-square-foot facility in Etna Green and a 50,000-square-foot facility in Elkhart, Ind. Winona has been continually exploring new capabilities and expanding its operations ever since.
Toying with the idea of powder coating tritoon boat rails and knowing the first hurdle was finding someone to handle the necessary lengths, Drudge had learned of Winona’s parts capacity — currently, the company has four production lines for powder coating; two at each facility. The part window can handle parts 34" x 72".
However, size of the parts wasn’t the real issue. Many people at Smoker Craft Inc. remained unconvinced that powder coating was the right solution given the post-forming of the rails. Typically, post-forming induces unusual stress in the coating and can result in defects. Undeterred, Drudge decided to get everyone involved in the same room for a serious deep dive into the possibilities.
The team at Winona were determined to rise to the challenge. Visker recalls the meeting with Smoker Craft Inc., “I said ‘We’re willing to go to the end to figure this out. If we can solve it, we will do it. We’ll do chemistry, we’ll look at powders — we’ll go everywhere we need to go.’”
According to Dennis Powell, business development manager for Winona, the working relationship with Smoker Craft Inc. was a two-way street in terms of open communication and collaboration. Powell says Winona was given free rein to explore every avenue and learn as much about Smoker Craft’s manufacturing process as necessary to understand how to approach the project. “We had all kinds of questions, and they just brought us into the process,” he says.
Drudge was impressed by Winona’s determination and persistence. “It was very apparent that they wanted it to work as badly as we did,” he says. “I feel like they did their homework.”
The right process
Winona looked at three key elements to achieving success: powder, pretreatment and product profile. Winona thought perhaps a powder meeting AAMA specifications for high performance and durability could be one possibility. As an AAMA-certified applicator, the company turned to its powder supplier,
AkzoNobel, to discuss the possibility of using one of its Interpon architectural powders.
“These are very robust coatings that are meant to weather harsh environments,” Dominic Gradozzi, regional manager, AkzoNobel says. “The challenge, as we work with the substrate and the pretreatment and the forces involved with bending that part, becomes how the coating can move with that part without compromising adhesion. This required a study between the forces of elongation, flexibility, hardness and the cohesive relationship between all those variables.”
AkzoNobel guided Winona to the AAMA 2604 powder class as it has the best post-forming characteristics.
Next, Winona altered the product profile to schedule only aluminum product on its dedicated line. This was key as it allowed for the pretreatment to be optimized for aluminum and prevented wide ranges in pretreat settings. The company worked with pretreat supplier Americo Chemical Products to dial in the washer chemistry.
“One thing that really made the difference was switching the chemistry to all aluminum on one of our lines — switching that to get a much more aggressive etch,” Visker says.
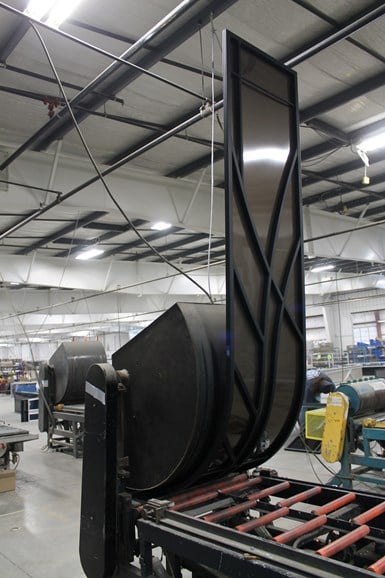
Approaching the problem from all sides
Larry Beals, vice president of Operations at Winona, guided the team in the application of Six Sigma methodology for the project — identifying defects, working to determine the cause, and improving the process to increase the quality and repeatability of results.
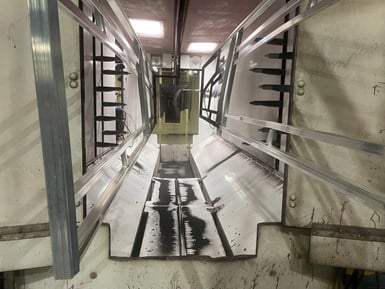
Rails undergoing powder coating process at Winona.
Assessment of the kinds of defects that were occurring during post-forming revealed two distinct failure modes: stress cracks in the bend radii, and vertical coating delamination in varied locations. The vertical delamination defects were consistent with gravitational flow associated with pretreat drainage.
“We used a thermal imaging camera,” Visker says. “We could actually look at the rails coming out of the dry-off oven and we could see if we had different variants in temperature.”
The thermal imaging camera allowed Winona to identify areas in the part that were trapping water. Visker explains that sending the part through a 350°F oven boils the water but the problem is that at the same time, it is evaporative cooling as well, meaning the part won’t reach 350° and therefore the powder will not be completely cured. Drain holes can address this kind of problem, but the location of a drain and getting a manufacturer to change their part design can oftentimes be tricky.
“We would go back to Smoker Craft and say you need to put a drain hole here,” Visker says. “If we hadn’t had a customer willing to modify their process, it wouldn’t have worked.”
Drudge adds, “That probably impressed me as much as anything because as soon as we started actually checking all the parts with the camera and you could recognize where the water was trapped, you figured out how to address the problem.”
Open communication is key
There are times when you must protect your intellectual property. However, when you are willing to be a little more open with the team that you’re working with, and with your partners on a project, there’s a good chance it’s going to facilitate things in a really positive manner. Involving your partners at earlier stages or opening those lines of communication has benefits.
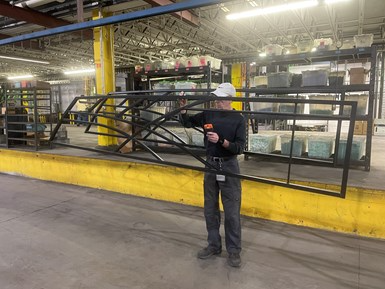
When Winona began the project with Smoker Craft, rework rates were at around 25%. Utilizing the Six Sigma methodology approach and working together, rework rates were reduced to almost zero. Today Smoker Craft has ramped up its production of tritoon boats featuring the powder coated rails. Roughly 75% of the boats are utilizing the new solution. Winona says at the time of this writing, it is coating parts for 175 boats a week and that number is growing.
The open communication that Winona and Smoker Craft Inc. has implemented for this project is a good example of what collaboration can achieve in manufacturing.
Powell says the project appealed to his background in engineering. “It really is a success story for cooperation at the earliest that you can. Not many people say, ‘Hey, if we’re doing something wrong, or we can do something better, you need to tell us.’”
Visker adds, “Everybody worked together. Whatever this project demanded, the challenge was met, everybody was in. It is a great success story.”
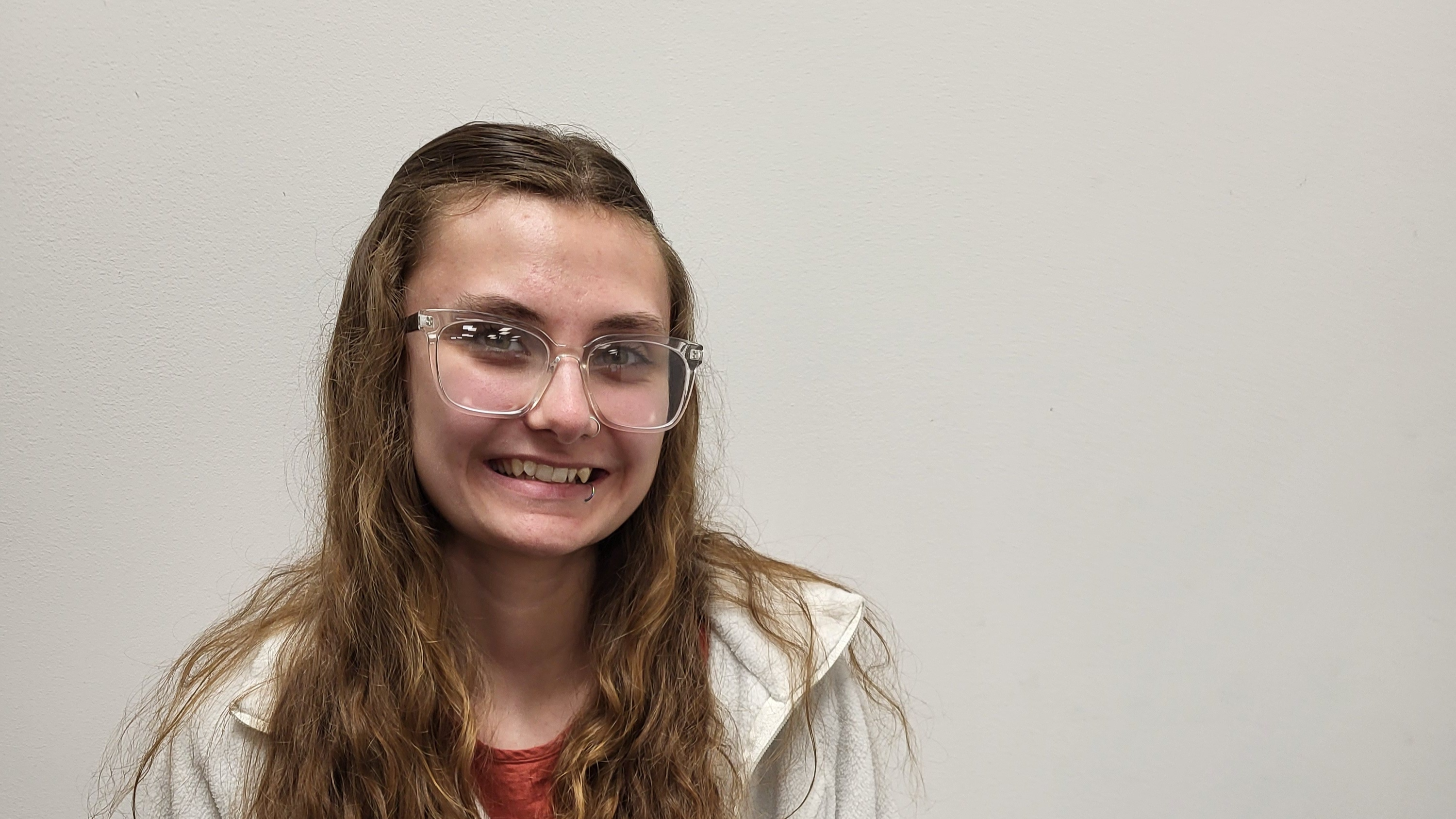